The process of mixing polyurethane spray foam involves the combination of two main liquid components: an isocyanate and a polyol resin. When these components are mixed together, a chemical reaction occurs, resulting in the formation of polyurethane foam.
Here’s a step-by-step overview of how the polyurethane spray foam process works:
- Components
- Isocyanate (Component A): This chemical compound reacts with the polyol to form the foam. Common isocyanates used in polyurethane foam production include methylene diphenyl diisocyanate (MDI)
- Polyol Resin (Component B): This is a blend of polyols, blowing agents, catalysts, surfactants, and other additives that determine the foam’s properties.
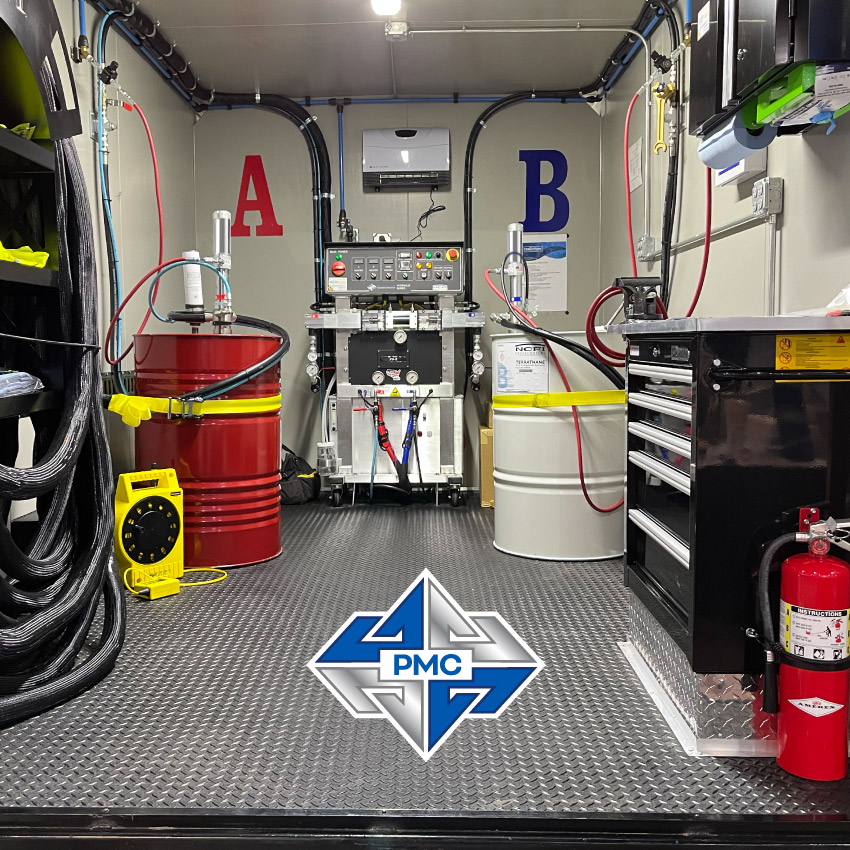
- Preparation and Equipment
- Storage and Handling: The isocyanate and polyol resin are stored in separate containers. They must be kept at the correct temperature and the two components are only mixed as they leave the spray gun during the application. Alternatively, some open-cell foams (component B) may be mixed with a pneumatic mixer in the drum before application, but still will never be mixed together with component A until leaving the gun during application.
- Mixing Equipment: Components A and B are pressurized and heated separately in a machine called a proportioner. They are then fed into the spray gun where they combine to form the spray polyurethane foam. The components are never mixed prior to reaching the gun.
- Mixing and Reaction of Polyurethane Spray Foam
- Metering and Proportioning: The equipment, called a proportioner, precisely meters and proportions the two components, ensuring they are mixed in the correct ratio, typically 1:1 by volume.
- Mixing: In the mixing chamber of the spray gun, the isocyanate and polyol resin are combined. This initiates the chemical reaction that produces polyurethane spray foam.
- Spraying: The mixed chemicals are sprayed onto the target surface. The mixture is typically under high pressure, which ensures thorough mixing and proper atomization.
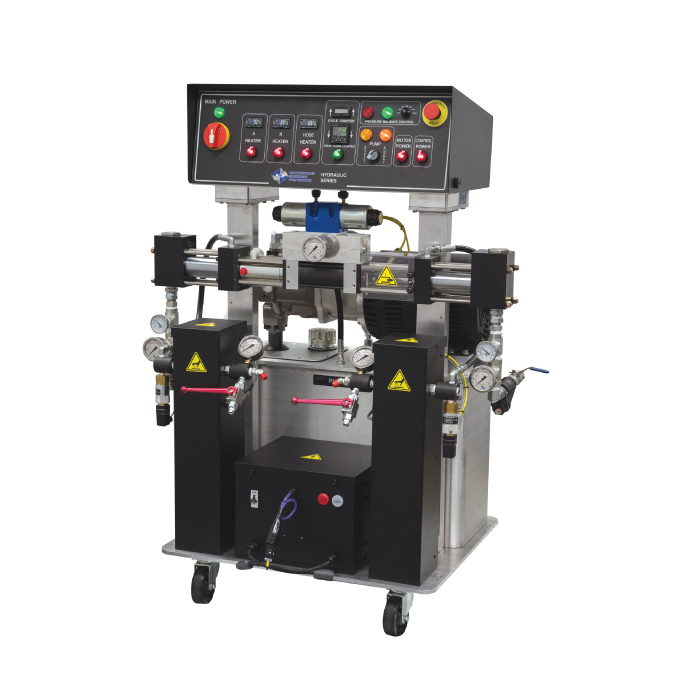
- Chemical Reaction and Expansion
- Exothermic Reaction: When the isocyanate and polyol resin mix, an exothermic reaction occurs, generating heat. This reaction causes the polyurethane foam mixture to expand. The speed of reaction depends on the B component predicates.
- Foam Formation: As the foam expands, it fills gaps, cracks, and cavities. Industry approved HFO blowing agents or water help create the foam’s cellular structure by forming bubbles within the mixture.
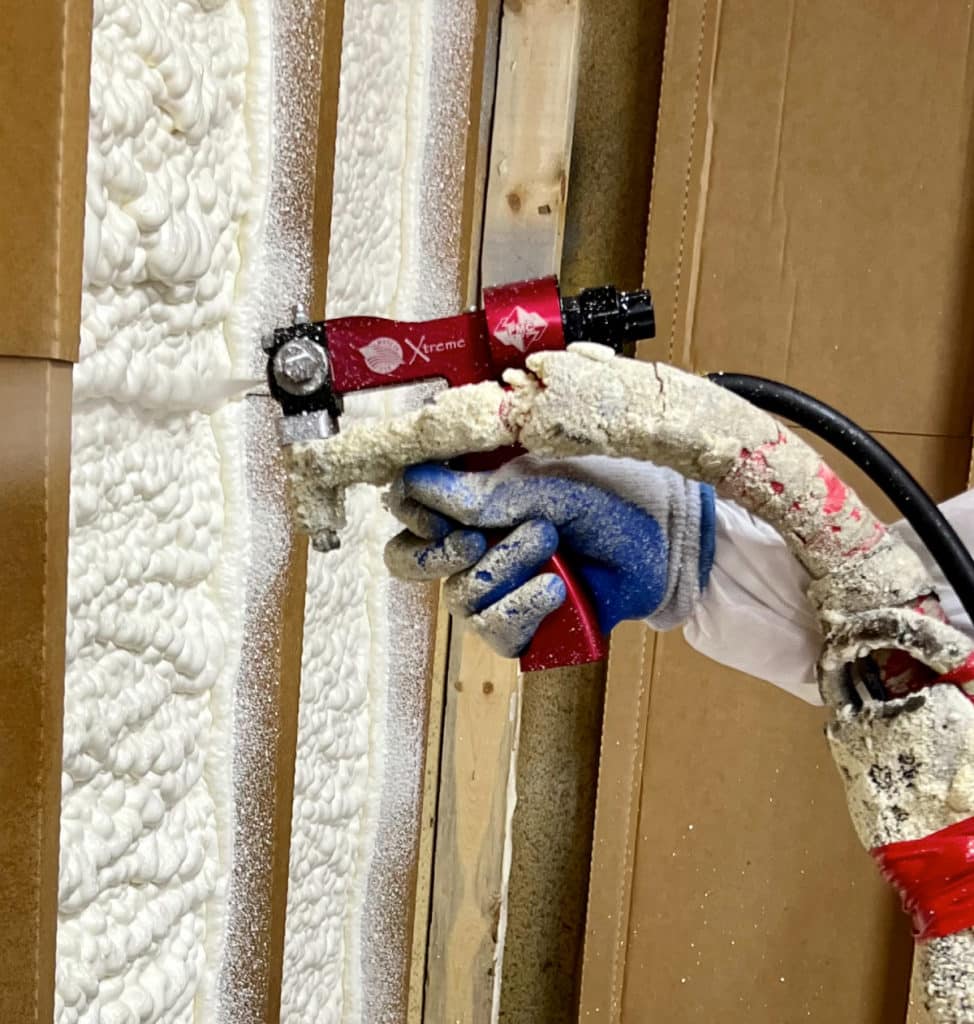
- Curing and Hardening
- Initial Expansion: The rate at which the polyurethane spray foam begins to expand upon spraying is dependent on B side component, and will continue to expand for a short period. Open-cell foam expands more than closed-cell foam thanks to its open cell structure.
- Setting: Different B side components will have a different tack, rise, and cream time, varying for application. Within a few minutes, depending on the formulation and ambient conditions the foam will set.
- Full Cure: The foam reaches its full mechanical properties after curing, which can take several hours to a day. During this time, the foam hardens and solidifies, forming a rigid or semi-rigid structure.
Types of Polyurethane Spray Foam
- Open-Cell Foam: This type of foam has a lower density and is softer and more flexible. It is often used for interior applications where sound absorption and insulation are desired. The cells within the foam are interconnected, allowing air to fill the spaces.
- Closed-Cell Foam: This foam is denser, more rigid, and has higher insulation properties. It is often used in exterior applications and areas requiring structural reinforcement. The cells are closed, making the foam more resistant to water and vapor infiltration.
Safety Precautions when using Spray Polyurethane Foam (SPF)
- Personal Protective Equipment (PPE): Applicators should wear appropriate PPE, including respirators, fresh-air systems, gloves, goggles, and protective clothing, to protect against exposure to chemicals and fumes.
- Ventilation: Adequate ventilation is necessary during the application to disperse any fumes and ensure a safe working environment.
- Training: Proper training is essential for applicators to handle the equipment and chemicals safely and effectively.
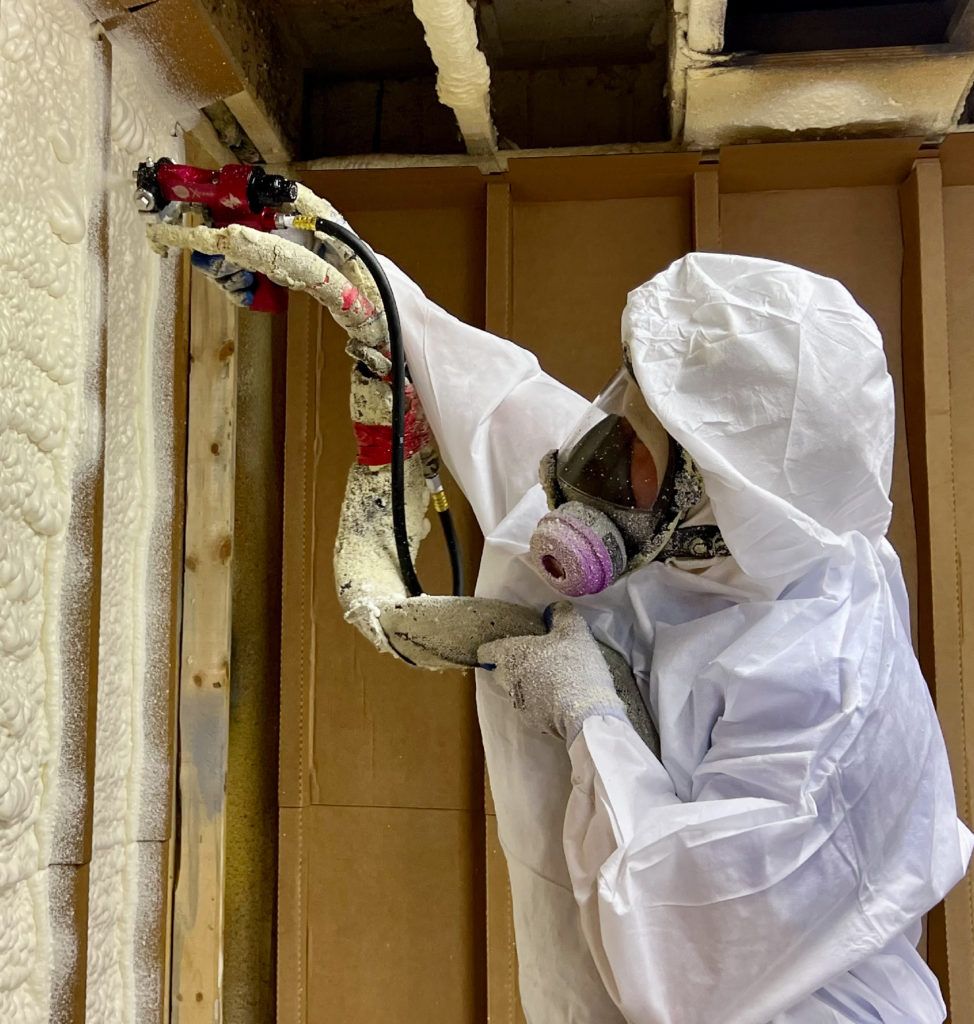
The process of mixing polyurethane spray foam involves precise metering, pressurization, and heating of isocyanate and polyol resin, followed by an exothermic reaction caused by the mixture which then expands and forms foam. It is important to understand this process and to be properly trained in the use of the proportioner, components, hoses and spray gun. Contact your PMC Machinery Distributor or contact us for more information.